
PDX Next – Portland Airport Expansion Project (2024)
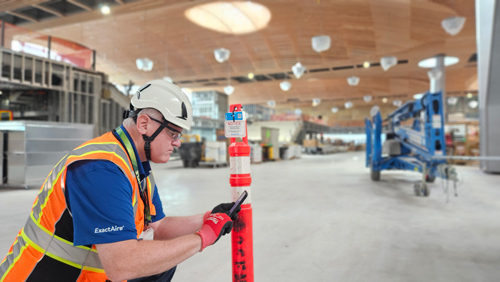
A POLYGON EMPLOYEE CHECKS REAL-TIME T/RH LEVELS, USING THE EXACTAIRE REMOTE MONITORING MOBILE APP
Source: Polygon; Credit: Kevin Lockard
Project Owner: Port of Portland (Airport)
Project Location: 7000 NE Airport Way, Portland, OR 97218
Completion Date: May 1, 2024
Architect/Designer: ZGF
Mass Timber Engineer/Manufacturer: TimberLab / Zip-O-Laminators
General Contractor: Hoffman Skanska JV
Structural Engineer: KPFF Consulting Engineers
Other Contractors: Polygon US
POLYGON PARTNERED WITH Hoffman Skanska JV to monitor and manage indoor environmental conditions for protecting mass timber and materials on PDX Next, the Portland Airport expansion project. Stakeholders wanted visibility and control of temperature and humidity for creature comfort and drying of construction materials, and continuous wood moisture content monitoring for mass timber. Polygon designed a comprehensive climate-control solution with temporary heat and ExactAire remote monitoring.
PROBLEM
Polygon needed to heat about 10 million cubic feet with 50-foot ceilings. They saw 3 problems with using direct-fired heat:
1. Finding and occupying outside space would be difficult.
2. Direct-fired heat uses outside air, which can lead to high fuel consumption and additional humidity.
3. Direct-fired heat produces fuel-hazardous by-products, like carbon dioxide, that can negatively impact people and the environment. This didn’t align with what Polygon knew about the environmental, social, and governance philosophy of the project.
As for the mass timber, the roof was being built in 20 sections outdoors. Although the beams were sealed, it was possible that moisture might get trapped, leading to mold. Conversely, heating equipment might cause overdryness, leading to checking or splitting. Polygon offered a more proactive approach to help avoid any potential problems.
SOLUTION
The first step was to deploy remote monitoring. Twenty-two ExactAire multisensors were installed to continuously record ambient conditions. Six were equipped with wood moisture equivalent (WME) probes and connected to beams.
A few months later, Polygon installed 5 fuel-efficient, 1 million-BTU heaters indoors. These produced and recirculated clean, warm air to over 60 degrees Fahrenheit. “Polygon set up a custom ExactAire system, online dashboard, and reporting process,” said Joel Bennett, project manager for Hoffman Skanska JV. “We can see if there’s an issue right away and, based on the location of the sensor, we can quickly hone in on the cause and get right to work on the solution. We also have the history and trendlines, which provide assurance that conditions are kept within the necessary ranges for our mass timber and finish elements. It’s great to be able to show, without any question, that conditions are right. It removes any doubt and helps us keep things on track and moving forward.”
BENEFITS
The combination of ExactAire and the right climate control gave stakeholders reassurance that the proper conditions were being produced, and they were able to communicate that information. This helped with managing schedule slips and helped to protect materials from poor conditions.
The trend logging from ExactAire serves as documentation and verification for future reporting. Should anyone question what conditions were at a given point in time, the project team will be able to share temperature, relative humidity (RH), and WME data.
A superior, efficient heating solution was provided because Polygon understood the trade-offs among the options, the requirements and limitations of the job and site, and the overall project goals.
Full case study: https://www.polygongroup.us/PDX
Download PDF