
Omega Factory (2024)
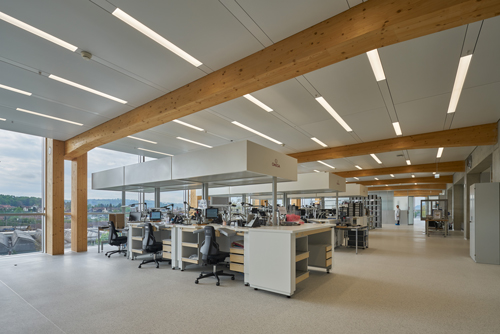
WATCHMAKING WORKSHOP
Credit: Didier Boy de la Tour
Project Owner: Omega S.A.
Project Location: Jakob-Stämpfli-Strasse 96 Biel/Bienne, Switzerland 2502
Completion Date: February 1, 2017
Architect/Designer: Shigeru Ban Architects
Mass Timber Engineer/Manufacturer: Création Holz AG, SJB Kempter Fitze AG (Timber Structural Engineer)
Structural Engineer: Schnetzer Puskas Ingenieure (General/Concrete Structural Engineer)
Mechanical, Electrical, and Plumbing: Gruner, Kiwi, Roschi+Partners, HKG Engineering
OMEGA WATCHMAKING DEMANDS specific performance criteria from a building for the sake of craftsmanship as well as employee health. To support the precision of the watchmakers’ work, their facilities must be evenly lit and dustfree, with minimal vibration. The 6-story Omega Factory is a hybrid structure composed of a rigid concrete core running the length of the middle third of the building, flanked by timber-framed watchmaking workshops and offices that are 10.5 meters deep. The core contains stairs, elevators, and restrooms, as well as an automated storage system known as the Central Stock. Two vertical lifts retrieve watchmaking components from an inventory of 30,000 boxes and deliver them directly to the watchmakers via conveyors.

FACTORY CONSTRUCTION
Credit: Philipp Zinniker / Itten+Brechbühl
SOUTHEAST FACADE WITH LOADING DOCK
Credit: Didier Boy de la Tour
Spruce glulam columns are spaced every 5.4 meters along the perimeter, and they’re connected to spruce glulam girders by two circular beech Laminated Veneer Lumber (LVL) dowels. The column-and-beam joints have no metal hardware, a feat that requires a high level of engineering and fabrication accuracy. The joints are similar to the elliptical beech dowel joints used at the Tamedia Headquarters (Shigeru Ban Architects, Zurich, Switzerland, 2013), but simpler because circular dowels are more industrial and less expensive to fabricate. In both buildings, beech—a hardwood—was selected for its superior rigidity.
The floor slabs have a hybrid approach as well. A 100 millimeter-thick, in situ, reinforced concrete topping was added to the Cross-Laminated Timber (CLT) structure to increase its weight, thereby reducing building vibrations. Pursuing a heavier building is counterintuitive—typically, it is less expensive and more efficient to design structures to be as light as possible—but watchmakers are highly sensitive to movement, warranting the addition.
Within a workshop, it is important to balance technical requirements with the employees’ comfort. Cleanliness is paramount for this type of production facility, and its clean room construction is unprecedented for a timber building. A significant volume of air exchange is needed to maintain a dust-free environment. Increasing a ventilation system’s speed of supply and exhaust is known to cause health concerns, such as those resulting from dryness. It also creates a noisy environment.
Perforated drop ceiling panels were designed to supply a great volume of air across a broad surface area at a slower speed. The air exhausts out at the floor level, creating one-way airflow to further minimize the circulation of dust.
The Omega Factory has a bright and open interior with ample daylight. The floor-to-ceiling glazing boasts stunning views of the town and landscape, a visual reprieve from the detailed tasks of watchmaking. To facilitate this work, the facade needed to be as clear as possible, with low-iron glass permitting unpolarized natural light. The glazing’s lack of color distortion has the added benefit of improving the timber structure’s visibility from the exterior.
Download PDF