
Putting Number to ‘It Depends’ (2023)
Emily Dawson, AIA, LEED AP
A look at cost trends emerging from a decade of mass timber projects in the US
Mass timber is attractive to designers and builders for so many reasons: “It makes us more collaborative!” “The environmental benefits are inspiring!” “It looks amazing!” “It even smells good!” However, answering the seemingly straightforward question “How much does it cost?” is anything but simple.
Cost-conscious clients drift back toward traditional methods and materials upon hearing “it depends.” So—even though it does!—being able to answer them with as much clarity as possible is crucial. We decided to ask another tough question: with examples of over 1,500 mass timber projects in the last decade in the US alone1 and with a growing community of designers and builders who have completed multiple projects, are cost trends emerging?
What if we zoomed out from the many details that make a mass timber project successful? Would we see patterns?
For answers, we asked architects, engineers, and builders with a depth of experience with mass timber projects to share statistics from their portfolios.2
As difficult as it is to compare apples and oranges, it is particularly valuable to understand cost differentials in relation to other primary structural materials: concrete, steel, and light timber or steel framing. When mass timber replaces concrete and steel construction, it usually generates greater savings than when it replaces light framing. The overall trends are similar for all three structural materials, however, so they are grouped together in this analysis.
What was immediately clear is that there generally is a premium for a mass timber project, up to 15 percent. But the median project premium was less than 2 percent, and the gap continues to shrink as teams and markets become more experienced.
These figures do not take into consideration mass timber buildings’ additional potential to capture more in lease rates and lower tenant turnover (see chapter 8 for more) or the advantage to the building owner’s return that results from shortened schedules. These calculations will not be apparent in a builder’s cost estimate, and the building owner can only investigate them accurately within their overall pro forma.
That said, understanding construction cost is foundational to any feasibility analysis. To gain insights on where project successes and struggles were occurring, we grouped cost information into the three macro systems that make up every building: (1) the superstructure, all above-grade structural components; (2) the substructure, all below-grade structural components and foun dations; and (3) the environment, which groups the building envelope, systems (mechanical, electrical, plumbing and fire protection (MEPF)), and interior finishes. Mass timber offers distinct advantages, challenges, and potential in each of these three categories.
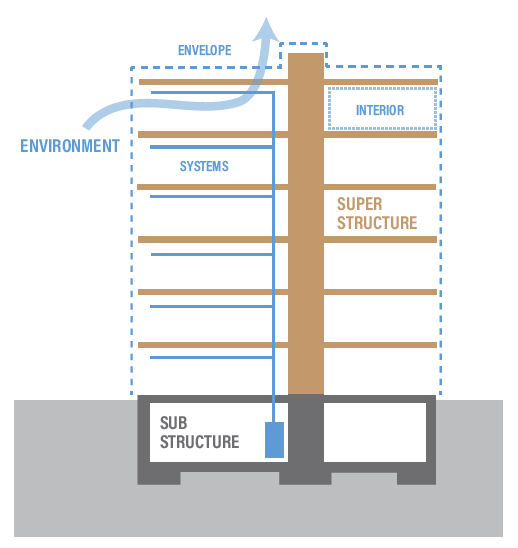
FIGURE 1: BUILDING DIAGRAM
Superstructure: The greatest cost savings are found in the superstructure’s construction schedule. The total construction schedule can be reduced significantly, up to 25 percent. Resulting cost reductions include overhead, carrying costs, earlier occupancy, and reduced risk. Contractors report significant cost savings in general conditions, even with increased levels of coordination. In fact, increased coordination is exactly what creates the greatest savings in the field.
Notably, these savings are often missed in a hard cost analysis of materials and labor. If the estimator understands labor savings, however, the findings can make an impact on early cost models. In a study of 100 mass timber buildings in the United Kingdom, Waugh Thistleton Architects found a 50 percent to 70 percent reduction in site staff for structural framing. The choice of lateral systems matters as well, and it can often drive the overall material and labor premium. Concrete cores may slow the overall schedule, for example, because the mass timber framing has to pause while the core is constructed. The fluctuation of the lumber commodity market presents another material cost challenge; tracking when to procure material can make a difference between an overall premium or savings. This is especially challenging when timber suppliers and fabricators are flooded with demand.
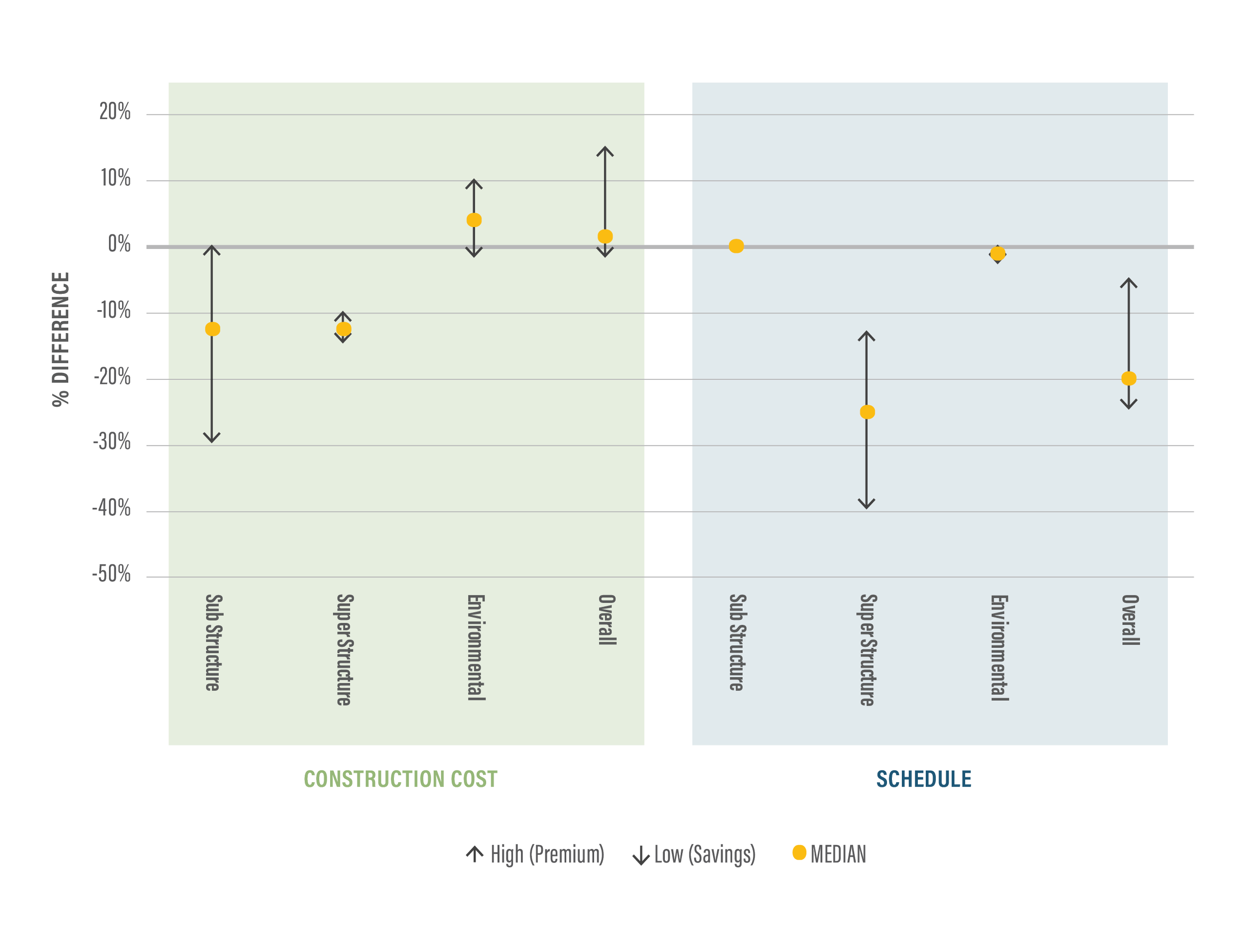
FIGURE 2: COST AND SCHEDULE DIFFERENCES BETWEEN MASS TIMBER AND OTHER STRUCTURAL MATERIALS
Substructure: Savings in foundations, when they occur, are seen primarily in hard costs. Because a smaller amount of concrete requires similar excavation, formwork, labor, and curing times as a greater amount, these savings are not likely to move the needle on a project with straightforward soils conditions. However, because a timber building on average weighs only 20 percent as much as a steel or concrete structure,3 the outcome can be quite promising when soils conditions are more complicated. Significant savings occur when a much lighter structure allows for less complex and costly foundation solutions. In these cases, total overall construction costs are likely to be lower than buildings with heavier structural systems. The savings are maximized for projects in high seismic zones, where the lighter mass timber structure translates to lower seismic forces that must be resisted by the foundations.
Environment: The vast amount of installed material that follows the construction of the superstructure creates the environment that makes a building comfortable to inhabit. Every project takes a different approach to the building’s envelope, MEPF systems, and interior finishes. Respondents’ cost reports in this category ranged from “usually more” to “often less” when compared to other structural systems. Although more exposed structural surfaces can mean savings on finishes, cost increases commonly stem from additional acoustic treatments and higher appearance criteria for drywall detailing and exposed mechanical components. Timber buildings over 12 stories may find no savings from exposing the structure because of the way fire protective encapsulation requirements are written into the code.
However, the building environment category may hold the most promise for the future of cost comparisons with other structural systems. When paired with a highly coordinated construction team, prefabricated enclosure, systems, and finish elements can take advantage of the superstructure’s rapid assembly superpower. In fact, highly modular projects can expect an overall schedule savings of up to 50 percent.4 As mass timber and modular industries mature, options for prefabricated finish and environmental systems components will multiply.
Taking a step back from the complexity of specific projects allowed us to see cost trends emerging. A 20 percent reduction in overall schedule is now the norm, driven by a 25 percent median schedule reduction in the superstructure. The slight overall cost premium seen across projects disappears when substructure and environment savings are also realized. Builders reported that cost margins are trending closer to negligible as the industry matures. Indeed, experienced teams more often reported cost neutrality or savings; premiums were more likely to occur with inexperienced partners. Another promising indicator that cost concerns may soon be a thing of the past is that many respondents reported in-progress affordable housing projects. Several also mentioned repeat clients and replicated projects, a true testament to project success. At this point, it is easy to imagine that “it depends” will soon be replaced with “Yes, it’s true—mass timber will save you time and money.”
1 https://www.woodworks.org/resources/u-s-mass-timber-projects/
2 The companies who participated reported on commercial projects in the United States.
3 https://www.thinkwood.com/blog/4-things-to-know-about-mass-timber
4 https://content.aia.org/sites/default/files/2019-03/Materials_Practice_Guide_Modular_Construction.pdf
Download PDF