
Green Canopy NODE (2024)
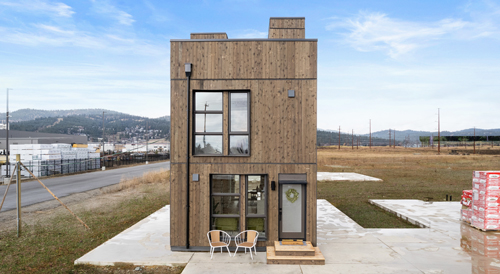
GREEN CANOPY NODE’S MASS TIMBER MODEL HOME IN SPOKANE, WASHINGTON, IS BASED ON THE INTEGRATED BUILDING KIT.
Source: Green Canopy NODE; Credit: Inside Spokane Photography
Project Owner: Green Canopy NODE
Project Location: 19202 Garland Ave, Spokane Valley, WA 99027
Completion Date: March 27, 2023
Architect/Designer: Green Canopy NODE
Mass Timber Engineer/Manufacturer: Mercer Mass Timber
General Contractor: Green Canopy NODE
Structural Engineer: Mercer Mass Timber
Mechanical, Electrical, and Plumbing: Green Canopy NODE
Other Contractors: Foust Fab and Erectors, Ameriwest Electric, Enertech Mechanical
THE MASS TIMBER Model Home encompasses prefabrication, logistics, and installation, helping validate Green Canopy NODE’s Integrated Building Kit. Components for the home in Spokane, Washington, were manufactured off-site and assembled on-site. The 1,200-square-foot, 2-story volumetric modular Cross-Laminated Timber (CLT) townhome with a rooftop deck has 2 bedrooms and 1.5 baths and was built in less than 100 days. The project aimed to prove out a new prefabricated building system capable of providing developers with a housing solution that reduces timelines, is scalable for mass production, and is cost-competitive in the market.
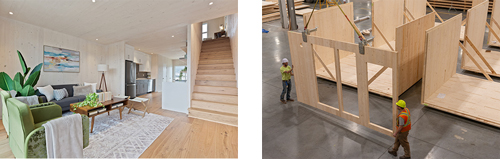
Left: THE INTERIOR OF GREEN CANOPY NODE’S MASS TIMBER MODEL HOME IS SPACIOUS AND WELCOMING.
Source: Green Canopy NODE Credit: Inside Spokane Photography
Right: WORKERS ASSEMBLE GREEN CANOPY NODE’S MASS TIMBER MODEL HOME.
Source: Green Canopy NODE Credit: J. Craig Sweat
In tandem with Green Canopy NODE’s commitment to sustainability, the Mass Timber Model Home catalyzes a net-zero transition. Its carbon-negative design and its Design for Disassembly (DfD) integrate seamlessly into the circular economy. It standardizes innovative technologies in the building components. Mass timber was chosen as the primary material because of its precision manufacturability, engineered structural qualities, and carbon storage capabilities, making it an ideal candidate for off-site manufacturing.
Compared to a stick-frame version of the home, the Mass Timber Model Home is 44 percent faster to complete, stores 6.6 times more carbon, and boasts a seemingly effortless 0.8 ACH airtight building envelope.
Integral to the project’s success is the deployment of Green Canopy NODE’s patent-pending Utility Kit system. Featuring 2 utility walls for the kitchen and bathroom, the kits are manufactured off-site and ensure streamlined on-site assembly and completion. With plumbing, electrical load centers, and mechanical systems preinstalled, the Utility Kits reduce construction time, requiring only 1 hour for wall installation, and shortening on-site mechanical, electrical, and plumbing (MEP) work. Plumbing connections require only 2.5 hours.
The utility walls plug into a raised floor system for rapid horizontal distribution of MEP throughout the home. To create the raised floor, the team used CLT offcuts to produce pedestals, thereby diverting material that would normally become waste. Additional innovation included Computer Numerical Control (CNC)-marked pedestal locations, which eliminated the need for measuring and increased the speed and efficiency of installation.
In essence, the Mass Timber Model Home exemplifies the efficiency and sustainability of the Integrated Building Kit and serves as a beacon for the future of housing, blending eco-consciousness with cutting-edge technology and construction practices.
Download PDF