Wednesday, March 26, 2025
Mass Timber in Industrial Design: Built Warehouse Case Studies
Oregon Ballroom 203Moderator:
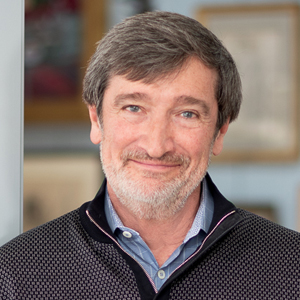
Disrupting the Industry-al Norm: The First Mass Timber Warehouse for a Key Player in the Real Estate Logistics Market
There’s an art to the traditional design and construction of an industrial building. The architectural firms, general contractors, and suppliers who work on these projects know the role that they play backwards and forwards, with two goals typically top of mind: affordability and schedule. While there may be site or code considerations that vary with each project, the roles, scopes, and assumptions are consistent. The technical aspects of designing these types of buildings tends not to be complex, and traditionally involves largely prefabricated steel and concrete construction.
If an industrial facility can be simply designed and constructed to meet demand for warehouse space…what happens when a forward-thinking industrial developer decides to try a mass timber facility? How does the “standard process” change?
CEO and Principal of ASPECT Structural Engineers, Adam Gerber will discuss considerations when shifting the “industrial” project approach to mass timber. Adam will be speaking to recent experience working with Prologis on their 250,000 sqft mass timber distribution centre, currently under construction in Ontario. He will highlight areas where existing industrial project approaches are well-suited to mass timber design, lessons learned that impact the project schedule, and “project kick-off” conversations that will set the team up for success.
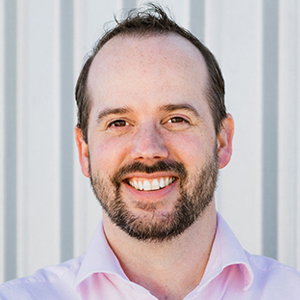
The Efficacy of an All-Timber Warehouse: Cost and Design Considerations for Large-Scale Manufacturing and Warehouse Facilities, Completed and In Construction
A two-person panel to include industry partners that have developed systems using engineered wood products for all-timber warehouse solutions.
1) Swinerton: William Silva will discuss design and cost considerations of using CLT products for the 206,000 sq ft CLT manufacturing facility they are building for Timberlab in Millersburg, Oregon.
2) Freres Engineered Wood: Kyle Freres will discuss the final design and cost considerations of a completed 60,000 sq ft warehouse constructed in Mill City, Oregon, that is made entirely out of Mass Ply Panels with LVL beams and columns.
Attendees will benefit from the experience of a well-researched exploration of timber warehouse constructions considerations, including best practices and lessons learned for completed and in construction warehouses and manufacturing facilities.
Built Warehouse Case Studies for Prologis
This presentation will explore Prologis’ efforts to find ways of incorporating mass timber design and construction for industrial warehouse developments. The presentation and panel discussion will include the opportunities, challenges, and lessons learned in mass timber applications for the industrial warehouse industry.
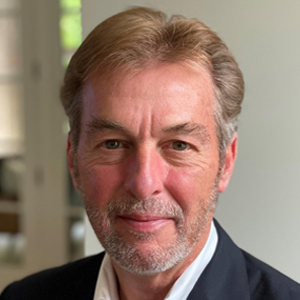
Building the Business Case for Mass Timber Industrial Assets
Industrial buildings are forecast for significant and ongoing growth underpinned by global trends such as online retail and data centres. This presentation examines the case study of a 15,000 sqm mass timber industrial building in Melbourne, Australia, for a publicly listed client (market cap USD $30 Billion). The presentation illustrates how, by connecting project deign/delivery and evolving market needs and institutional investor considerations, mass timber construction provides new avenues for project opportunities.
For AEC entities, and commercial developers and investment professionals, this presentation also provides a template for the future direction of mass timber’s deployment in this sector.
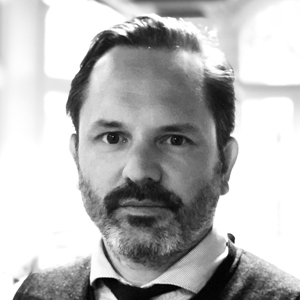
Session CEUs: Course Description & Learning Objectives
Course Description
Industrial buildings have long adhered to established norms prioritizing affordability and speed through traditional steel and concrete construction. This course explores how mass timber challenges those conventions and redefines industrial development design and construction processes. Using real-world case studies from experts leading groundbreaking mass timber warehouse projects across North America and globally, attendees will gain insights into the opportunities, challenges, and lessons learned in adopting mass timber for industrial applications. The presentation will provide attendees with a comprehensive understanding of the transformative potential of mass timber industrial design by addressing key considerations for cost, design, sustainability, and market viability.
Learning Objectives
- Understand and examine mass timber’s sustainable attributes, including carbon sequestration potential and reduced environmental impact compared to traditional industrial building materials.
- Identify how shifting from steel and concrete to mass timber alters design and construction approaches for industrial facilities, including material performance, code compliance, structural design, and prefabrication strategies.
- Assess the financial and scheduling impacts of using mass timber for large-scale warehouse projects, based on case studies and lessons learned from completed and in-progress developments.
- Review the impact an exposed wood structure has on the occupants compared to traditional structures through the principles of biophilic design.