
Mass Timber Systems: Evolving from Building Products to Product Platforms (2022)
Ryan E. Smith, Washington State University, and Mod X
Ivan Rupnik, Northeastern University, and Mod X
Tyler Schmetterer and Mod X
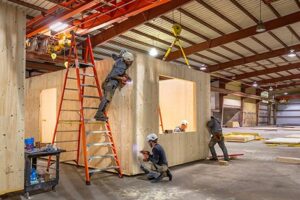
FIGURE 1: THE FORTERRA MODULAR CLT PROTOTYPE 2022 IS AN EXAMPLE OF MASS TIMBER PRODUCTS EVOLVING INTO MASS TIMBER SYSTEMS
Source: Forterra
1. INTRODUCTION
The number of mass timber structures continues to grow internationally as the resource, design, testing, manufacture, and assembly supply chains evolve to meet demand. The growing importance of the annual International Mass Timber Conference (IMTC) is evidence of this progress, and it’s indicative of the escalating need for networking and knowledge-sharing in the industry. As part of this growth, stakeholders in the mass timber supply chain are evaluating how to increase value from manufacturing building products and structural components, including Cross-Laminated Timber (CLT) and glulam. They aim to strengthen the value-add of subassembly manufacturing and of integrating mass timber into off-site construction systems (Figure 1). This article addresses the knowledge gap at the intersection of building products and off-site systems by identifying key concepts and explaining how they apply in practice to off-site and modular construction. Selected case studies are cited.
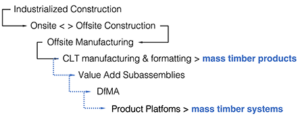
FIGURE 2.1: KEY CONCEPTUAL RELATIONSHIPS IN MASS TIMBER SYSTEMS
Source: MOD X
2. KEY CONCEPTS IN MASS TIMBER SYSTEMS
Numerous terms, definitions, and concepts are rapidly being established in the mass timber industry. Mass timber systems are part of an expanding off-site construction practice—the application of manufacturing-oriented processes.1 This section will identify and define key concepts in manufacturing- based construction and how they relate to mass timber systems (Figure 2.1).
2.1 INDUSTRIALIZED CONSTRUCTION
Industrialized construction is the application of the principles and production methods of industrial manufacturing, including advancements in digitalization, automation, lean construction planning and management, data management, and materials science. The goal is to attain increased productivity.2 These principles can be applied to on-site (e.g., 3D printing) and off-site conditions (e.g., Housing and Urban Development [HUD] manufactured housing). The most successful applications of these principles have resulted in industrializing the off-site and onsite aspects into a continuous whole to increase productivity and optimize labor and materials.3 Industrialized construction is a term widely used internationally. It’s also applied specifically in the United Kingdom (UK), where it has become synonymous with modern methods of construction (MMC)—the application of the principles of modern planning and processes.4 Mass timber construction sometimes utilizes an industrialized or MMC approach to project delivery.
2.2 OFF-SITE CONSTRUCTION
Off-site construction occurs when some portion of a physical building is completed off-site in an enclosed environment.5 It’s often assumed that off-site construction in the US is also industrialized, but there is ample evidence of off-site construction employing small-scale to zero industrial means, methods, and technology. Conversely, some instances of highly industrialized construction approaches are completed on-site (e.g., production housing). Conflating industrialization and off-site construction has resulted in market assumptions that productivity is achieved by moving construction under a roof, an idea that has rarely proven out in practice. On the other hand, highly developed off-site construction companies based internationally perform aspects of construction on-site precisely because they have industrialized the entire process and can accurately calibrate the cost-to-benefit ratio of on-site versus off-site scope-of-work (SOW) decisions. In the US market, the terms “factory-built,” “prefabrication,” “and off-site manufacturing” are often used interchangeably, with “off-site construction” as the more general term.6 These designations, however, are manufacturing-specific and represent a distinct step in the value chain of off-site construction project delivery. Off-site construction, therefore, constitutes the entire process of design, planning, manufacture, and site assembly of elements that have been prefabricated off-site.7 Mass timber products are manufactured in a factory environment, but they are infrequently produced in the service of off-site construction delivery.
2.3 VALUE-ADD AND SUBASSEMBLIES
Although established principles and practices from the manufacturing industry are seldom used in the construction industry, they are crucial when considering industrialized and off-site construction strategies. Within the construction supply chain, traditional on-site construction requires procuring materials and products that are manufactured, transported to a site, and assembled by trades in piecemeal fashion. As off-site construction continues to gain market penetration, materials and products may undergo value-add in a manufacturing or fabrication stage, during which enhancements are produced to create subassemblies before shipping and site assembly. Subassemblies are the 1D, 2D, and 3D value-add elements (e.g., panels and volumes) that are produced in a factory8 with enhancements beyond structure alone (i.e., insulation, exterior cladding, interior finishes, mechanical, electrical, and plumbing [MEP], etc.). Subassembly manufacturing may include modifying 1D elements into 2D elements (e.g., open panels) and/or modifying 1D/2D elements into 3D volumetric modules with systems integration. The value-add may be completed by an upstream or downstream supply chain partner, such as a mass timber manufacturer completing the next stage of an enhancement, an existing volumetric modular manufacturer integrating mass timber products into the production process, or a general contractor (GC) setting up a manufacturing operation to self-perform and self-supply mass timber subassemblies for in-house and third-party projects. A new segment of start-up manufacturers is adding value to materials and products by developing subassemblies. Mass timber is starting to integrate value-add enhancements and systems, including 2D panelized and 3D volumetric modules for the off-site construction supply chain (Figure 2.2).
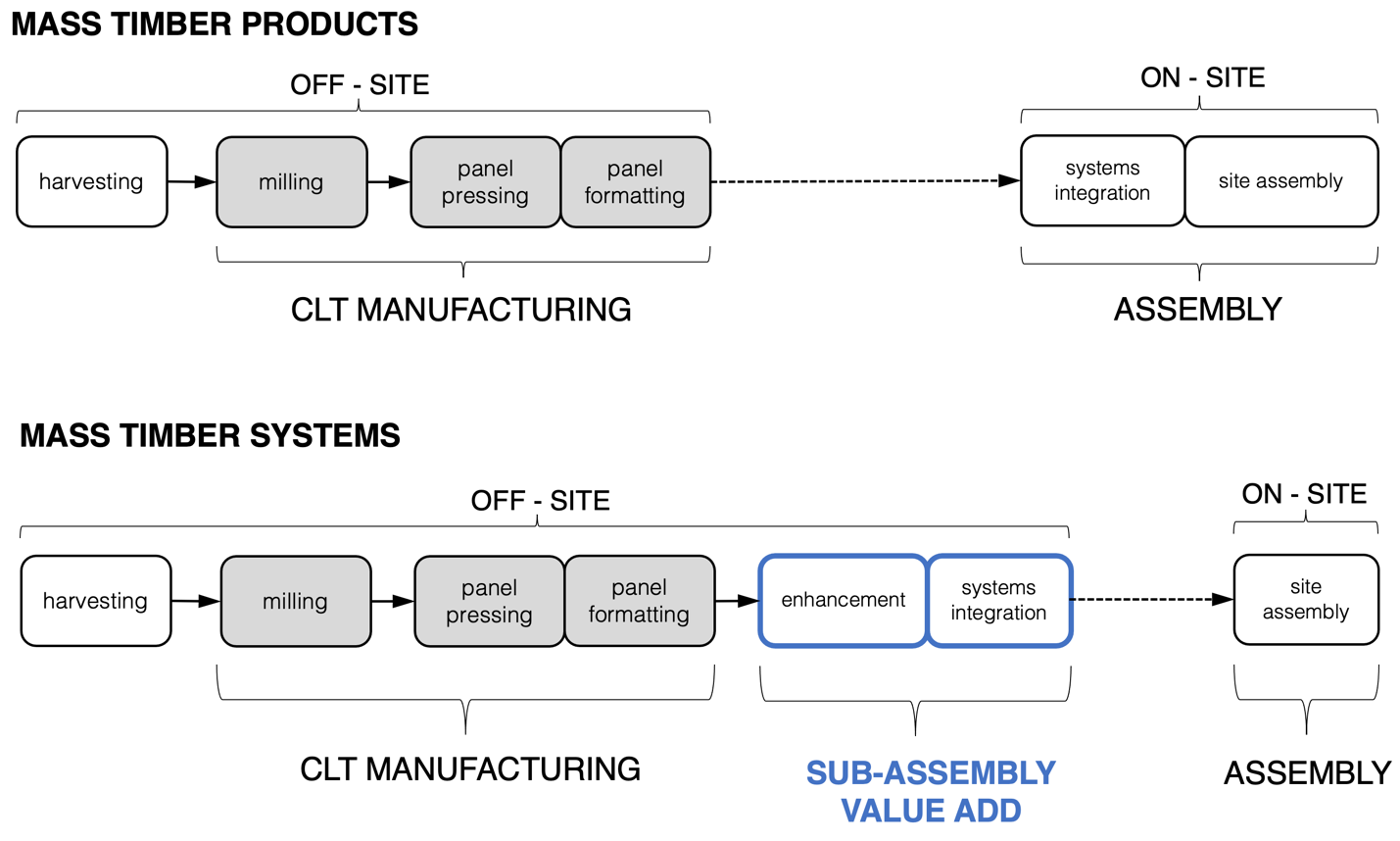
FIGURE 2.2: MASS TIMBER SUPPLY CHAIN RELATIONSHIPS IDENTIFYING OFFSITE VALUE-ADD MANUFACTURING AND ON-SITE ASSEMBLY
Source: Adapted from T. Beyreuther, Mass Timber Systems
2.4 OPEN VERSUS CLOSED SYSTEMS
Much of the manufacturing of mass timber products, particularly CLT and glulam, consists of the production of bespoke structural components to serve the needs of a specific, one-off project. These components can be conceived of as open systems— systems configured in many ways to produce different buildings.9 The raw manufacturing of CLT panel blanks, or standard dimensional production output, is an effective illustration of an open-system component. In this context, mass timber is the product of a manufacturing and supply process that is easily integrated into the framework of conventional construction. As the construction industry migrates toward on-site and off-site industrialized methods in planning, manufacturing, and assembly, mass timber components can increasingly function as part of closed systems—systems in which form and structure are two aspects of a single design process.10 In this manner, mass timber products can be differentiated from mass timber systems in off-site manufacturing, adding value and specificity to a closed system of construction.
2.5 DESIGN FOR MANUFACTURE AND ASSEMBLY (DfMA)
In the US construction industry, developers, GCs, and some Architecture, Engineering, and Construction (AEC) professionals are practicing a form of closed system design on a project-by-project basis through the application of Design for Manufacture and Assembly (DfMA) principles. DfMA doesn’t follow the traditional sequence of project documentation in construction, where means and methods are often finalized late in the process. Instead, DfMA requires early decisions and coordination, often sharing detailed Building Information Modeling (BIM) descriptions among the entire project team to determine the form of manufacturing and assembly that will be used.11 DfMA is distinguished by the awareness, objectives, and planning of what will be factory-produced versus site-assembled and the labor and workforce skills required to execute the respective work scopes.12 To gain the maximum benefits of DfMA, subassembly manufacturing of closed systems using mass timber products may be employed to attain some or all of the productivity strategies of industrialization and off-site construction.
2.6 PRODUCT PLATFORMS
The DfMA approach is a significant improvement over the standard model of coordination among project teams and manufacturers, especially when applied to large, unusual, and complex structures. In the context of residential housing, hospitality, commercial offices, industrial structures, and other typologically repeatable structures, a higher degree of design coordination is possible within the framework of industrialized off-site construction via the development of product platforms. An essential organizational tool in all product manufacturing industries, product platforms are defined as a collection of modules or parts that are common to a number of products (or buildings) and developed intentionally to achieve desired effects to create value.13 While the term “standardization” has historically had negative connotations in AEC communities building platforms can support a high degree of variability by reusing (part) variants that are interchangeable across multiple configurations to achieve an economy of scale without standardizing the product (or building).14 In summary, standardization at the part or component scale allows for more variety at the product or building scale.
Product platforms integrate subassemblies and processes that support products designed for manufacture, assembly, and variable configuration within a given framework. This process of predesign is what distinguishes product platforms from project- based DfMA, and it more accurately describes how smartphones and automobiles are designed and manufactured. A product platform may be developed based on a single project, but an investment in customer data input, digital design standards, manufacturing, and construction feedback loops is required to improve the platform so subsequent projects can realize their full potential.15 This continual improvement cycle is why the approach is often used by vertically integrated companies or joint ventures among stakeholders in the supply chain that collaboratively develop a platform for multiple projects within a consistent group. The approach does not require full vertical integration and offers the inherent value that end users are not required to be familiar with the nuances of a particular manufacturing and assembly process, but work within a well-established framework of developers, developer- builders, or designer-developer-builders.16
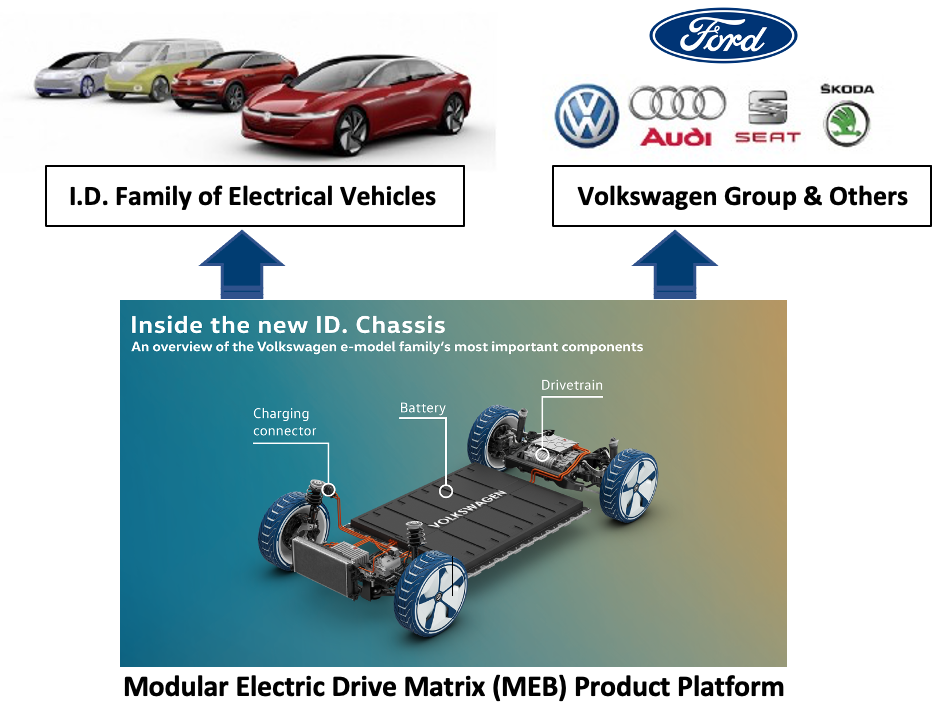
FIGURE 2.3: VOLKSWAGEN ELECTRIC DRIVE MATRIX (MEB) PRODUCT PLATFORM
Source: Volkswagen
Product platforms optimize the need to standardize manufacturing and assembly processes with the needs of specific sites and building programs. In this setting, product platforms are the backbone of mass production and bespoke customization or mass customization.17 While product platforms benefit from vertical integration, particularly during the formative period, they also provide companies the opportunity to separate and outsource aspects of the manufacturing and assembly processes to other subcontractors or suppliers because the parameters of the subassemblies that make up the product platform are clearly specified. Product platforms not only support the synchronous interchangeability of some subassemblies; they also support the continual improvement of subassemblies over time at variable rates from one another. Volkswagen has embraced this type of manufacturing innovation. The world’s second-largest car maker is heavily investing in the future of mobility with a transformative product platform called the modular electric drive matrix (MEB) to supply a modular chassis for electric vehicles (EVs) across several models and brand categories (Figure. 2.3).18 By 2028, it will launch almost 70 new e-models to the market while the platform will serve as the foundation for 15 million to 22 million vehicles worldwide.19 Further demonstrating the potential impact and flexibility of this type of product platform concept, Volkswagen is licensing the technology to competitive automotive manufacturers, including Ford, Fisker, and various EV startups. That way, it can amortize the cost of the platform research and development, decrease barriers to EV market entry, and further accelerate EV market penetration to reduce global CO2 emissions and support corporate sustainability objectives.20
In addition to the potential for interchangeability of subassemblies, product platforms can offer this feature to end users throughout the life of the structures. One of the most compelling illustrations of interchangeable flexibility in the world of off-site construction is the post-occupancy variability of Sekisui Heim homes in Japan that offer homeowners kitchen and bath upgrades in addition to disassembly and relocation of entire structural building volumetric modules. Sekisui Heim has been able to support Japan’s ambitious national goals of sustainability and a circular economy while also creating a significant secondary market of goods and services to its existing loyal customers by using the inherent principles of their half-century-old and continually improving product platform.21
Product platforms are a relatively new concept in the construction industry, accurately describing key conceptual and organizational foundations of manufacturing logics. Without the application of product platforms, no form of construction can realize the productivity potential of industrialized and off-site construction. Further, product platforms are essential to recouping the initial capital-intensive investment of migrating construction off-site, and the acquisition of state-of-the-art mechanized and automated production tools common to mass timber product manufacturing. Conversely, product platforms are a crucial strategy to insulate manufacturers and building stakeholders from the risk of overly productizing building structures (i.e., overstandardization) that cannot adjust to changing market demands, customer preferences, supply chain disruptions, regulatory changes, and future needs.22 Building on the forthright Farmer Review of the UK Construction Labour Model, a 2016 report commissioned by the British government that declared “Modernise or Die,”23 the construction industry and the growing mass timber industry will need to “modularize or die” through the development of product platforms to successfully migrate from mass timber as a building product to mass timber as a building system.
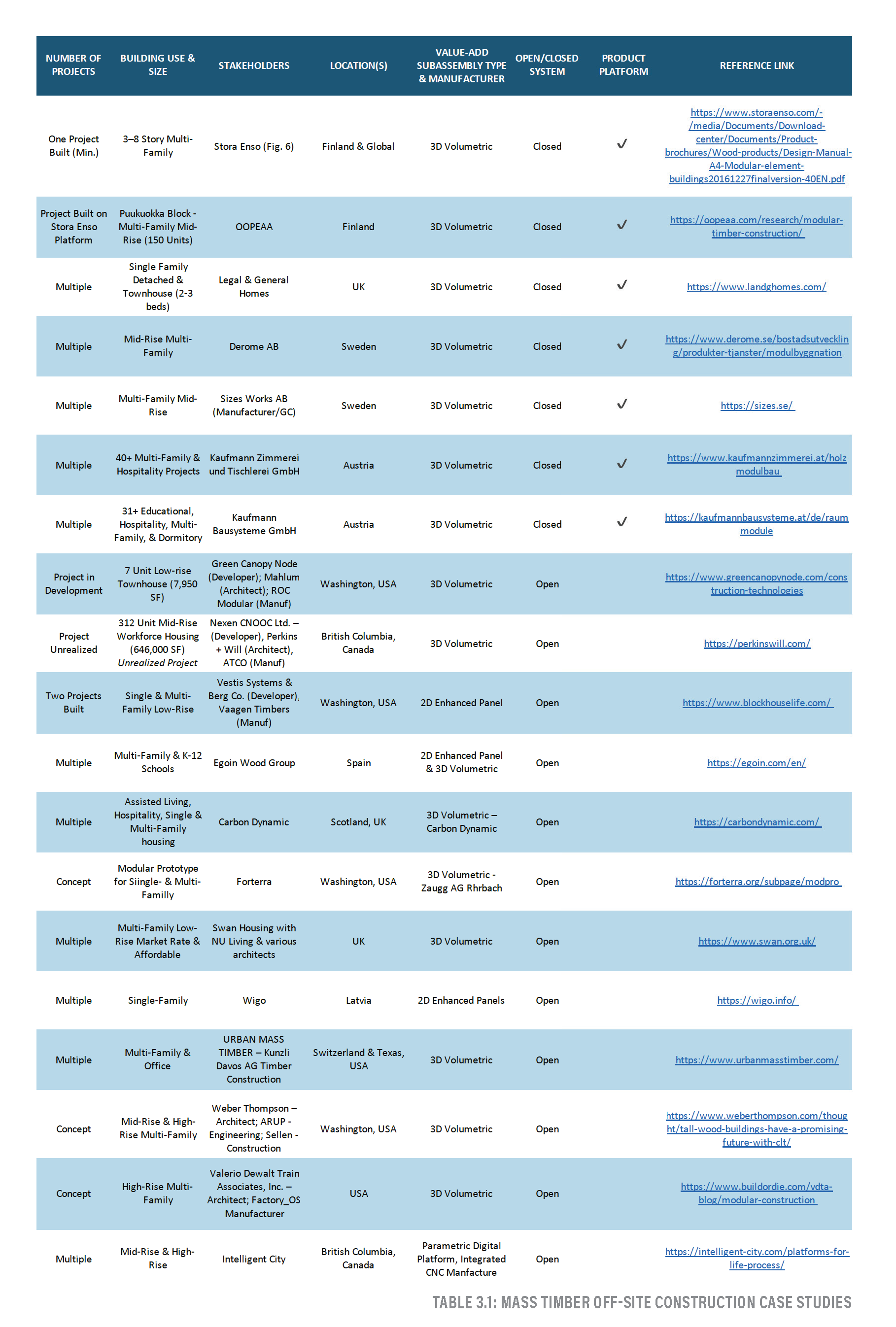
TABLE 3.1: MASS TIMBER OFF-SITE CONSTRUCTION CASE STUDIES

FIGURE 3.1: STORA ENSO MODULAR BUILDING SYSTEMS PROPOSES A CLT-BACKED SUBASSEMBLY FOR VOLUMETRIC MODULAR PRODUCTION THAT CAN BE CONFIGURED AND ASSEMBLED INTO DIFFERENT BUILDING PROJECTS
Source: Stora Enso
3. CASE STUDIES
The case studies table lists several projects that use mass timber products and leverage subassembly manufacturing and off-site construction methods. The subassembly system for each project is identified as a concept, prototype, single project, or multiple projects. Each also includes the subassembly: 2D enhanced panel or 3D volumetric; open versus closed system; and whether it’s a product platform (Table 3.1).
Reviewing this collection of case studies, it’s evident that mass timber is largely being deployed as a building product. The use of mass timber in projects requires stakeholder teams to accommodate an alternative design and construction approach (and DfMA in some cases), but it does not fundamentally modify project delivery modes. Mass timber is primarily manufactured for one-off conventional construction projects, but it is being considered as part of a value chain in an industrialized off-site construction system with subassembly manufacturing enhancements for improved productivity. To leverage the potential of mass timber products, mass timber supply chain stakeholders— developers, architects, engineers, mass timber manufacturers, subassembly manufacturers, and site assemblers/GCs—should consider how to develop mass timber as an integral strategy in the development and delivery of product platforms.
Although several business alignments may achieve positive results, off-site construction and product platform delivery are proving successful in vertically integrated or joint-venture supply chains where the platform investment can be utilized, amortized, and improved across several projects for quality control, cost control, and timeline reduction. As such, the specific supply chain company that performs the value-add subassembly manufacturing may vary. It might be an existing supply chain partner such as a CLT manufacturer moving down the supply chain to produce subassemblies or a GC moving up to create value-add elements with mass timber products (e.g., Timberlab). Mass timber subassemblies could also be supplied by an existing panelized or volumetric manufacturer willing to integrate mass timber products into its production line (e.g., ROC Modular). Finally, several start-up subassembly manufacturers and suppliers are focused on value-add, with more expected to follow in this rapidly developing sector.
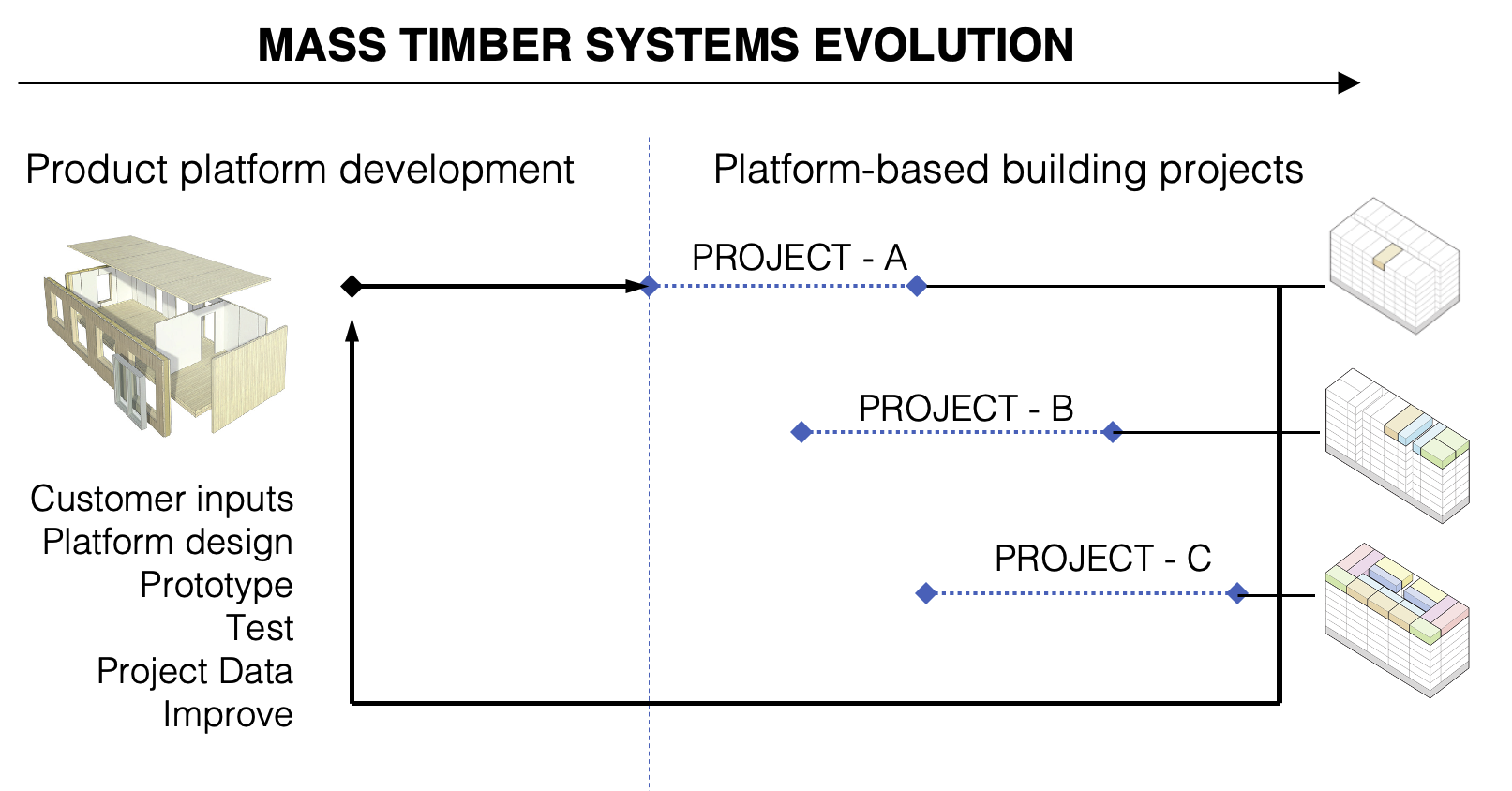
FIGURE 3.2: PRODUCT PLATFORMS ARE PREDESIGNED WITH CUSTOMER INPUTS AND RESEARCH APPLIED TO MULTIPLE BUILDING PROJECTS WITH A POST-OCCUPANCY FEEDBACK LOOP TO CONTINUOUSLY IMPROVE THE PRODUCT PLATFORM
Source: MOD X
An illuminative case study focused on developing a clean and openly accessible product platform concept is called Building Systems by Stora Enso: 3-8 Storey Modular Element Buildings.24 Stora Enso developed a CLT-based 3-story to 8-story residential building platform intended for designers, contractors, building owners, and developers (Figure 3.1). In this system, the subassembly is the CLTbacked floor-, wall-, and roof-enhanced panel elements that are configured into various volumetric modules to be shipped and assembled on-site. The product platform approach of the 2D enhanced panel subassembly integrates into a volumetric modular subassembly and, thereafter, different projects. A single product platform is intended to serve many different projects as a configurable and adaptable system that is continuously improved (Figure 3.2). The 2D subassembly to be standardized with a high degree of flexibility and variability in configuring volumes for customization of a particular project application, demonstrating the evolution of mass timber products in the supply chain from a bespoke structural element assembled onsite to an integral product for the development of a subassembly platform as a building system.
To address this opportunity for mass timber systems, the 2022 IMTC included a new track developed by conference partner MOD X that focuses on off-site and industrialized construction and housing. MOD X will create, coordinate, and moderate a series of four panel discussions as a specialized educational track during the conference and coordinate a local off-site manufacturer tour in April 2022. MOD X will also moderate an interactive panel discussion and virtual factory tour during the IMTC virtual extension day in May 2022. The sessions in the offsite track are designed to address the needs identified in this article for an evaluation of mass timber as product, platform, and system, and they address the following topics: value-add supply chains, product platforms and modularization in off-site construction, appropriate digitalization and automation, and business models in industrialized housing.
1 Barbosa, F., Woetzel, J., & Mischke, J., Joao, M.R., Sridhar, M., Parsons, M., Bertram, N., & Brown, S. (2017). Reinventing Construction: A Route of Higher Productivity. McKinsey Global Institute. Available at: https://www.mckinsey.com/~/media/mckinsey/business%20functions/operations/our%20insights/reinventing%20construction%20through%20a%20productvity%20revolution/mgi-reinventing-construction-a-route-to-higher-productivity-full-report.pdf (Accessed: 01/29/22).
2 Al-Hussein, A. (No Date) International Journal of Industrialized Construction. Available at: https://journalofindustrializedconstruction.com/index.php/jic/about (Accessed: 01/24/22).
3 Barbosa, F., Woetzel, J., & Mischke, J., Joao, M.R., Sridhar, M., Parsons, M., Bertram, N., & Brown, S.(2017). Reinventing Construction: A Route of Higher Productivity. McKinsey Global Institute. Available at: https://www.mckinsey.com/~/media/mckinsey/business%20functions/operations/our%20insights/reinventing%20construction%20through%20a%20productivity%20revolution/mgi-reinventing-construction-a-route-to-higher-productivity-full-report.pdf (Accessed: 01/29/22).
4 Davies, A. (2018) Modern Methods of Construction: A Forward-Thinking Solution to the Housing Crisis? Royal Institution of Chartered Surveyors (RICS). Available at: https://www.rics.org/globalassets/rics-website/media/news/news–opinion/modern-methods-of-construction-paper-rics.pdf (Accessed: 01/24/22).
5 Smith, R.E. & Quale, J.D. (2017). Offsite Architecture. Oxon and New York: Routledge. p. 264.
6 Operation Breakthrough (1976). Operation Breakthrough: Lessons Learned About Demonstrating New Technology. U.S. Government Accountability Office. Available at: https://www.gao.gov/assets/120/117465.pdf (Accessed: 01/27/22).
7 National Institute of Building Sciences. (No Date) Off-Site Construction Council (OSCC). Available at: https://www.nibs.org/oscc (Accessed: 01/27/22).
8 Hairstans, R. (2015). Building Offsite: An introduction. Architectural design Scotland. Available at: http://www.ads.org.uk/wp-content/uploads/Building-Offsite-An-Introduction.pdf (Accessed: 01/27/22)
9 Peters, T. (1996). Building the Nineteenth Century. Cambridge: The MIT Press. p. 220.
10 Ibid.
11 Gao, S., Jin, R. & Lu, W. (2020). Design for Manufacture and Assembly in Construction: A Review. Building Research & Information, 48:5, 538-550.
12 Lu, W., Tan, T., Xu, J., Wang, J., Chen, K., Gao, S., & Xue, F. (2021). Design for Manufacture and Assembly (DfMA) in Construction: The Old and the New. Architectural Engineering and Design Management, 17:1-2, p. 77-91,
13 Harland, P.E., Uddin, Z. & Laudien, S. (2020). Product Platforms as a Lever of Competitive Advantage on a Company-Wide Level: A Resource Management Perspective. Review of Managerial Science, 14, p. 137–158.
14 Martin, T. (No Date) All You Need to Know About Modularization. Available at: https://www.modularmanagement.com/blog/all-you-need-to-know-about-modularization (Accessed: 01/29/22).
15 Muffatto, M. & Roveda, M. (2002) Product Architecture and Platforms: A Conceptual Framework. International Journal of Technology Management, Vol. 24, No. 1, p. 1-16.
16 Johnston, J. (2018) Platforms: Bridging the Gap Between Construction and Manufacturing. Bryden Wood (UK) Available at:https://www.brydenwood.co.uk/filedownload.php?a=13711-5ff83f3c65188 (Accessed 01/29/22).
17 Smith, R.E. (2019) Mass Prefabrication: Investigating the Relationship Between Prefabrication and Mass Customization in Architecture. Ch.14, Mass Customization and Design Democratization, Koleravic & Duarte (Eds.) London & New York: Routledge Taylor & Francis.
18 Volkswagen, AG (2022). Modular Electric Drive Matrix (MEB). Available at: https://www.volkswagen-newsroom.com/en/modular-electric-drive-matrix-meb-3677 (Accessed, 02/04/22).
19 Volkswagen, AG (2019). Available at: https://www.volkswagen-newsroom.com/en/press-releases/volkswagen-plans-22-million-electric-vehicles-in-ten-years-4750 (Accessed, 02/04/22).
20 Duke, S. (2021) VW Group platform strategy key to e-mobility rollout. Available at: https://www.just-auto.com/news/vwgroup-platform-strategy-key-to-e-mobility-rollout/ (Accessed, 01/29/22)
21 In 2008, 10 major home providers in Japan introduced a certification system called Sumstock for existing off-site manufactured homes to alleviate homeowner safety concerns including earthquake resistance and potential defects. This effort includes the upgrade of interiors and the entire relocation of volumetric modules. In 2018, MOD X witnessed firsthand the disassembly of a Sekisui Heim house that was being relocated in Tokyo. Additional information available at: https://japanpropertycentral.com/real-estate-faq/sumstock-certification-for-existing-homes/
22 Jensen, P., Lidelow, H., Olofsson (2015) Product Configuration in Construction. International Journal of Mass Customisation, Vol. 5, No.1. Inderscience Enterprises Ltd: p. 73-92.
23 Farmer, M. (2016). Modernise or Die. London, Construction Leadership Council. Available at: https://www.cs-ic.org/media/2846/mark-farmer-modernise-or-die.pdf (Accessed, 01/24/22).
24 Stora Enso (2016). Building Systems by Stora Enso: 3-8 Storey Modular Element Buildings. Available at: https://www.storaenso.com/-/media/Documents/Download-center/Documents/Product-brochures/Wood-products/Design-Manual-A4-Modular-element-buildings20161227finalversion-40EN.pdf (Accessed 01/24/22).
Download PDF